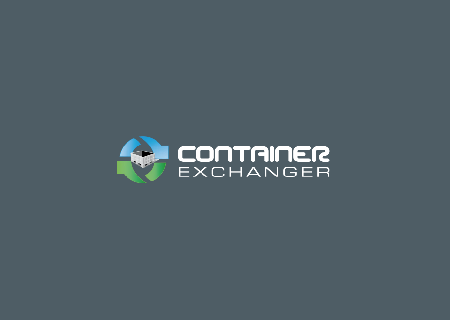
Extended Producer Responsibility: Manufacturers to Collect, Recycle, Reuse Packaging
The United States of America has been no stranger to the concept of recycling and reusing products and packaging. The practice of recycling has been around in this country for more than three decades. Introduced in the 1970s, recycling is believed to be one of the oldest and most important cornerstones of the environment movement that garnered mass media attention toward the late 80s and early 90s...
Read More