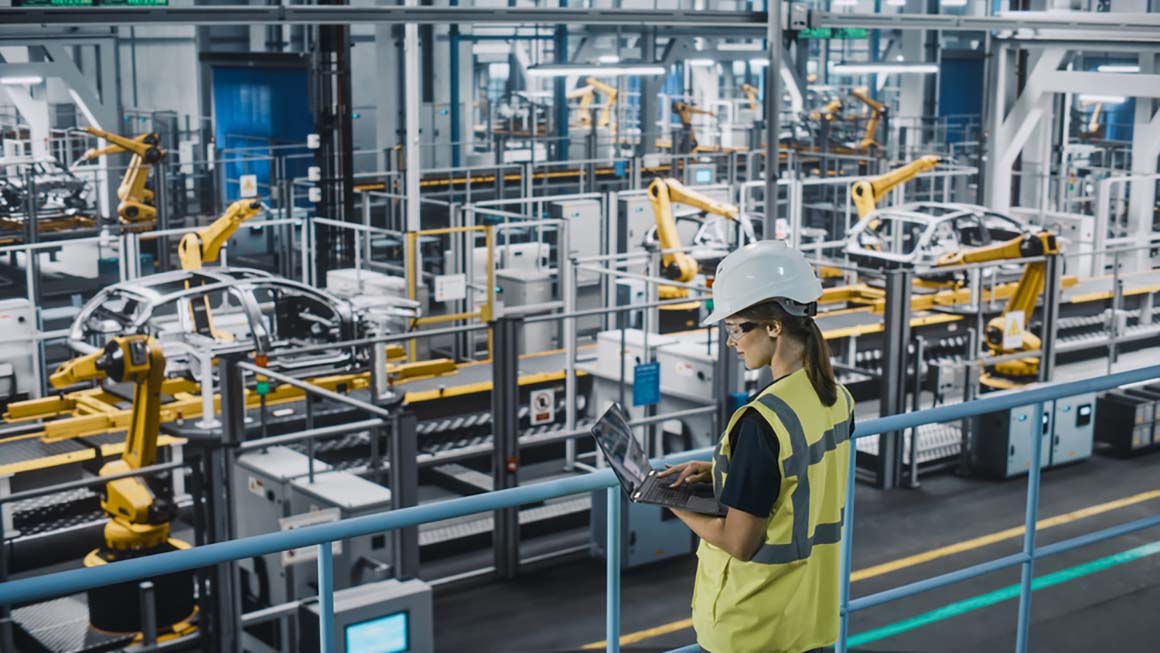
What Is the Automotive Supply Chain Process?
Nearly every modern economic sector is information-intensive, but the automotive industry might just take the cake in that regard. Automotive manufacturing companies need thousands of different parts to finish complex manufacturing processes to put high-caliber vehicles on the road. As a result, the automotive supply chain is vital to keeping things going in many parts of the economy. Additionall...
Read More