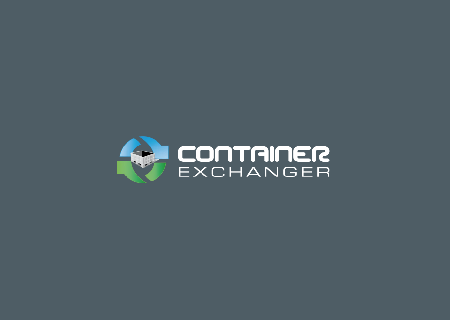
Grain Silos: What Are They and How Do They Work?
If you eat a bowl of cereal or piece of toast for breakfast, you are eating food made from grains. And, if you’re curious, you might have wondered how these grains made it to your table. Well, they originated from farms all across the world. Each year, farmers harvest millions of tons of grain and some of the grains are sold to food processors while others are stored for future use in grain silo...
Read More